Cheap and abundant Marcellus Shale gas derived from US fracking technology helps to drive competitiveness for a wide range of industries in the United States. This is especially true for the US Steel industry, and MATCOR’s recent project in Western Pennsylvania in the rolling hills of the Monongahela Valley is a great example of this.
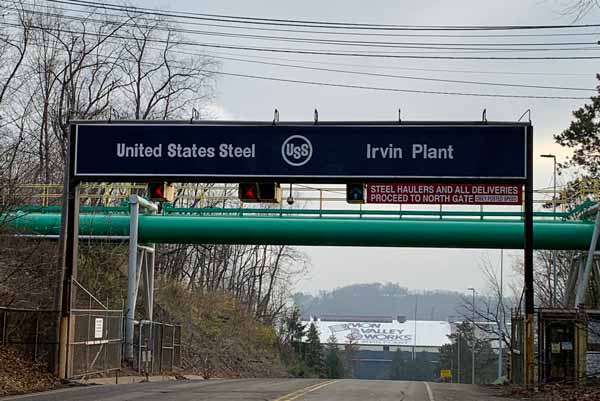
Nestled on a hilltop 250 feet above the valley is US Steel’s Mon Valley Works–Irvin Plant. This hot strip mill in the Pittsburgh West Mifflin suburbs first opened in 1938. The hilltop site required more than 4.4 million cubic yards of earth to be moved, more than any other project other than the Panama Canal. In May of 2019, US Steel announced plans to invest $1 billion dollars at the site to expand it and to build a cogeneration power facility expected to be operational by 2022.
MATCOR was selected by US Steel to install, commission and test an impressed current cathodic protection system to protect the critical coke oven gas (COG) product pipelines mixed at the West Mifflin COG facility. The coke oven gas is a mixture of commercial natural gas and recovered waste coke gas. This blending of natural gas with recovered gas reduces costs and improves US Steel’s energy efficiency. The pipeline, affectionately called the Green Monster, traverses the valley feeding various facilities. Mostly above grade, the pipeline goes below grade in numerous locations.
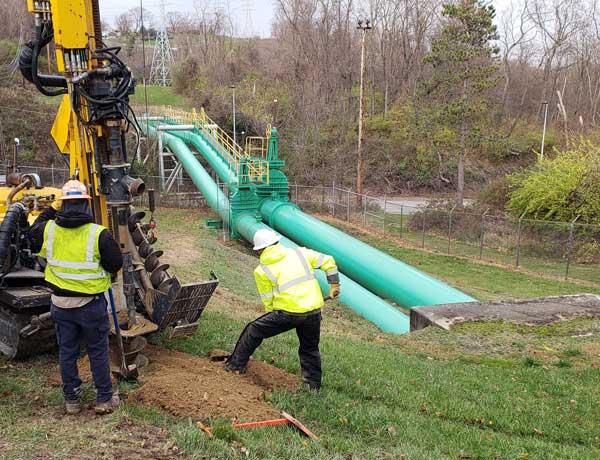
MATCOR’s MMP 3605 mixed metal oxide based canister anodes were selected as the new cathodic protection system anodes to protect the buried piping. Fifteen anodes were installed in individual 20-foot depth augered holes and connected to a #2 HMWPE buried header cable requiring approximately 1500 linear feet of trenching. The project included site specific safety training, regular coordination with site personnel and site restoration (seed, straw and fertilizer) after completion of the installation.
The project was a tremendous success and MATCOR is proud to have been able to partner with US Steel for their buried pipe corrosion protection.